Hot Melt Extruder
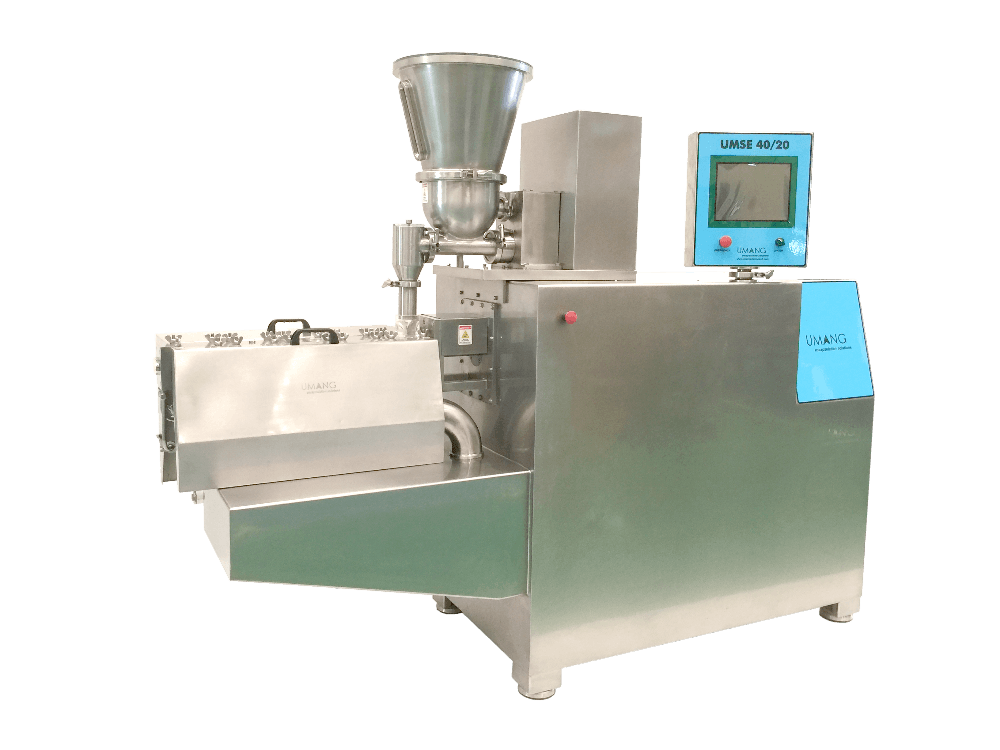
Product Information
Purpose
Working Principle
In this procedure, the raw materials are fed into the main hopper with the aid of a quantitative feeder, followed by a twin screw mechanism that ensures even conveying combined with segmented heating progressively rising in temperature until they get fused on-going through the system. After that, they pass through a programmable orifice plate all along their course as warmth decreases gradually.
The outcome
A firm, dense strip, which is then cut and sheared by a downstream system into uniform sizes granules. Hence, time is saved, steps are cut down, and reproducibility is improved through this complete one-step transformation from raw material to finished granules.
Key Features
Our recently developed One-Step Solid Dispersion
Versatile Feeding System
Supports a variety of materials via vibrating feeders and twin-screw feeders, ensuring flexible and precise dosing.Efficient Heating
Dual-zone segmented electric heating for upper and lower barrels ensures even and consistent thermal distribution.Accurate Temperature Control
Multi-stage feedback system maintains stable heating within ±0.5°C, ensuring process reliability and repeatability.Live Extrusion Monitoring
Real-time current monitoring and torque feedback protect the twin-screw, enhancing its lifespan and optimizing process safety.Dual Cooling Mechanism
Integrated water and air cooling helps maintain consistent temperatures and stabilizes output quality.Modular Twin-Screw Design
Combines multiple functions—mixing, pressurizing, melting, extruding, and cooling—to ensure full fusion of actives and excipients.Custom Orifice Plates
Offers flexibility with interchangeable extrusion dies for different material properties and desired output shapes.Multi-Stage Venting
Strategically placed vents release air and moisture during melting, reducing extrusion pressure and enhancing final product quality.Customizable Shearing Device
Adjustable shearing heads allow for the production of uniform granules, tailored to different formulation needs.GMP Compliant & User-Friendly
Easy to disassemble and clean, meets GMP standards, offers three-level password access, and features PLC automation with data logging and USB export.Expandability
Supports continuous wet granulation for additional flexibility in processing techniques.
Specifications-models-main technical parameters:
Model | ME-D16 | ME-D36 | ME-D50 |
Capacity(Kg/h) | 0.5-5 | 5-20 | 15-50 |
Total power(KW) | 10 | 30 | 50 |
Extrusion speed(rpm) | 20-600 | 10-500 | 10-300 |
External dimension(mm) | 2050*700*1560 | 3250*800*2500 | 3500*2250*2000 |
Total weight(Kg) | 700 | 1200 | 2500 |